SCM-Packaging types in logistics: primary, secondary, and tertiary
The type of packaging used for a specific product has implications that go beyond the protection of the merchandise. The size, material, and design of the packaging directly impact costs linked to storage and transportation, not to mention the effect that the aesthetic appearance has on the customer. Therefore, decisions concerning the choice of primary, secondary, and tertiary packaging are of marked strategic importance for a company.
In our article, we’ll go over the key concepts for choosing product packaging from a logistics point of view. What are the differences between primary, secondary, and tertiary packaging? What’s the role of each one?
Different kinds of packaging: primary, secondary, and tertiary
Product packaging involves various layers of materials, classified as follows:
- Primary, sales, or consumption-unit packaging
Primary packaging contains, stores, and protects a product. It is in direct contactwith the item and serves to maintain it in optimal conditions. This packaging designates the smallest consumption unit, facilitating the unit sale of the merchandise. It takes on very diverse forms: cans, jars, sacks, bottles, bags, etc.
Primary packaging carries out the following functions:
- Identify the product in line with current regulations and display the instructions for use, as well as other essential data such as the expiration date.
- Identify the brand and increase consumer appeal (depending on the product).
- Ensure the merchandise remains in a stable position in its sale location in the store (make sure it doesn’t fall).
- Guarantee that the contents are isolated.
- Protect the goods using the minimum possible material.
- Secondary or grouped packaging
Secondary packaging consists of the grouping together of primary packaging. It adds more protection and facilitates the marketing of the product on a larger scale. This packaging mostly comprises cardboard boxes, although they can also be plastic. For example, in the case of milk, an individual carton would be primary packaging, while the cardboard box containing the pack of cartons would account for secondary packaging.
Secondary packaging is tasked with the following:
- Be resistant to stacking (in the warehouse and at points of sale) and to handling during transportation so as to protect the product from damage.
- Contain a specific amount of product.
- Attract customers’ attention, especially for secondary packaging intended to be sold directly to the general public.
- Tertiary packaging
Tertiary packaging includes primary and secondary packaging to, thus, create larger unit loads, the most common forms of which are pallets, containers, and the modular cardboard boxes that they contain.
The functions and characteristics of tertiary packaging comprise the following:
- Remain stable and enable loads to be stored compactly.
- Leverage the storage capacity of the installations and industrial vehicles.
- Be authorized for use and made of resistant materials.
- On occasion, tertiary packaging can also perform a significant role in relation to the brand’s image. This is especially true for e-commerce logistics, where the box or packaging employed in transportation is tertiary and can include visual brand elements. An example of this is Amazon’s easily recognizable parcels.
In this logistics context, the significance of the unit load should be noted. It’s the basic unit that a company uses in the transportation and storage of its products. These loads can be in the form of pallets, boxes, containers, drums, reels, large recipients for bulk commodities (IBCs), sacks, big-bags, and the like. Various unit loads can exist in a single warehousing facility; they can be differentiated by area and stored in different types of racking adapted to each one.
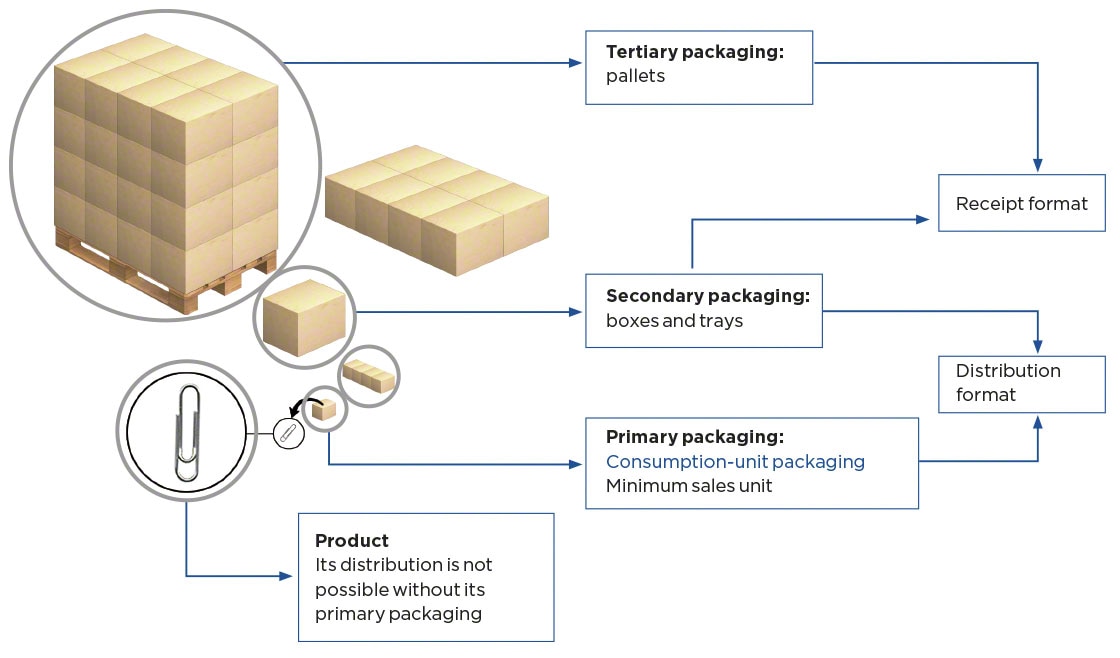
Factors that determine packaging choice
Choosing the best type of packaging aims to cut direct costs (purchase of materials, and waste management) and indirect costs (packing process, handling, storage, and losses due to damage). The main aspects that condition the selection of different types of packaging are:
- Product characteristics, such as state (liquid, solid, or gas), weight, volume, fragility, hazard level, value, stability (whether it becomes deformed or remains rigid), and whether or not it is perishable.
- The manufacturing and packing process will determine what types of primary and secondary packaging should be chosen. These will also have different formats according to whether the packing is done manually or automatically.
- Handling in transportation and storage involve multiple factors to be taken into account. These include: the stacking height the packaging needs to withstand, the time during which the parcels will be stored, the various transportation methods employed by the company (which can cause vibrations that affect the product), the number of times the items will be loaded and unloaded, whether or not the packaging is used in reverse logistics (for example, certain types of secondary packaging are prepared to be reused with e-commerce returns), and the temperature and environmental humidity to which the packages are subjected in storage and transportation operations.
- The environmental impact of the waste generated by the packaging, and the options to recycle or reuse it.
- Points of sale, as it’s necessary to consider where the packaging will be placed in the physical establishment and how it will have to be handled. On the other hand, in the case of online businesses, it’s a good idea to enhance the unboxing experience, since this is the first physical contact between the customer and the brand and product.
Packaging management strategies
According to the report The Empty Space Economy from Forbes Insights, a quarter of the space in each container and packagesent and received every year carries … air! Consequently, 66% of executives surveyed believe that they could achieve savings of at least 25% of the budget invested in packaging by eliminating that empty space.
Several of the strategies below are geared towards accomplishing this:
- Standardization of packaging measurements
One of the main advantages of standardizing measurements is the space saved in all supply chain phases, including production, transportation, and storage. For example, theGrocery Manufacturers’ Association or GMA pallet is widely used as a basic tertiary packaging solution for compact load storage in the US.
From there, another improvement to implement is the agreement between suppliers, logistics providers, distributors, and points of sale to choose packaging with dimensions corresponding to the modular size. These would be multiples of the GMA pallet), for example, 24” x 20” (1/4 pallet), 24” x 40” (1/2 pallet), and so on. This optimizes the stacking of boxes on the pallets and allows you to make the most of the space available in warehouses and transportation vehicles.
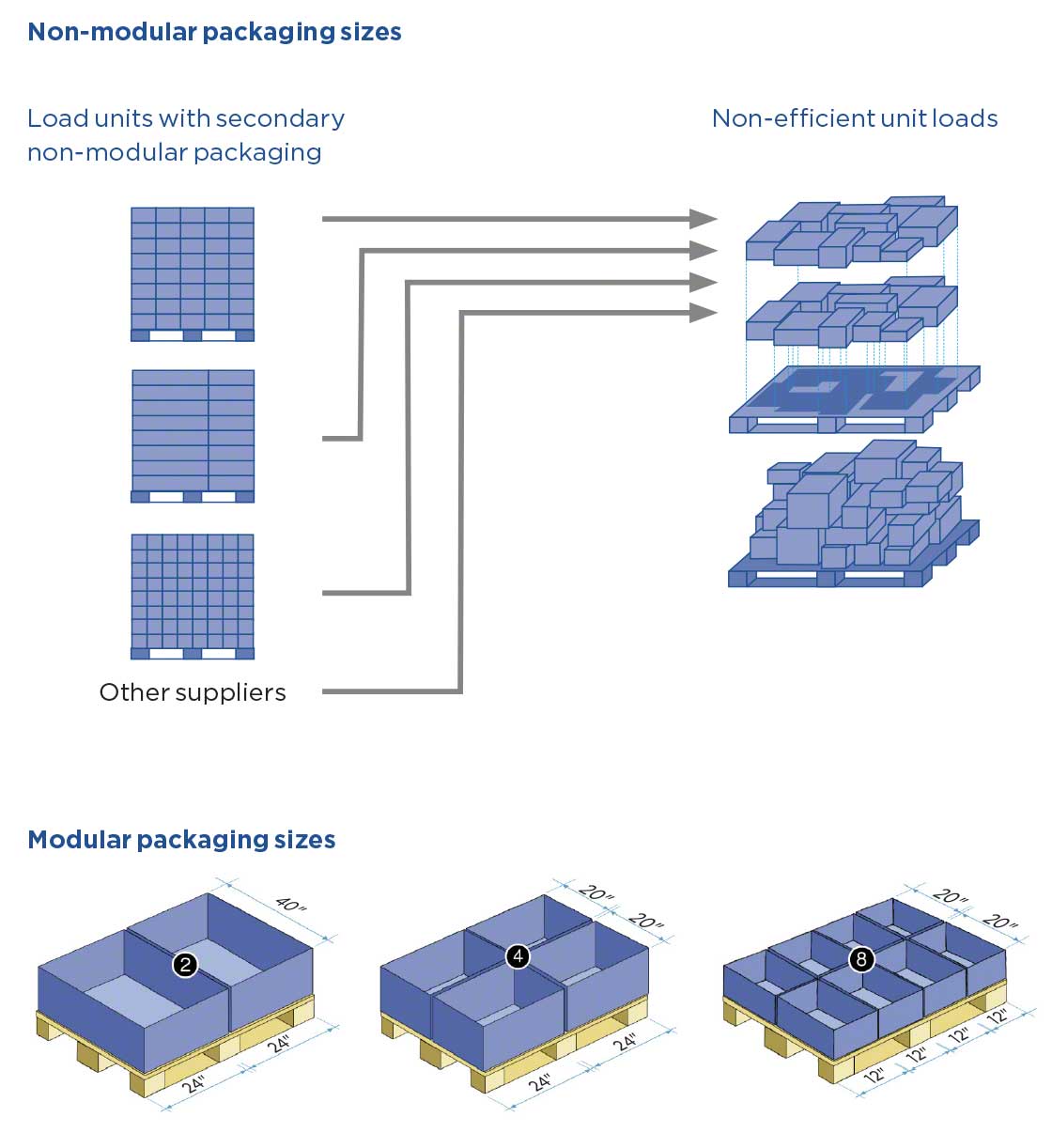
- Automate the selection and handling of packaging material
The starting point lies in analyzing your inventory characteristics to find basic measurements that are modular (that is, multiples of the GMA pallet, such as those indicated above) and can efficiently house the products stored.
And we can’t overlook an extremely important variable when it comes to transportation costs: dimensional weight, that is, the calculation of the space a package occupies in a vehicle in relation to its weight. The transportation agencies use this as a guide for setting their rates when packages are light yet bulky.
In this sense, the warehouse management system is integrated with the pallet checkpoints, scales, automatic labelers, and cobots that aid in the packing process. Based on inventory data, the WMS indicates to operators which type of packaging they should select to prepare each order.
Packaging for more efficient logistics
To identify points to improve in packaging management, it’s advisable to classify the various types of primary, secondary, and tertiary packaging and analyze how and who would be affected by a possible modification to each of them.
In industry, it’s a good idea to assess the optimization level of the packaging in terms of the material it’s made of, transportation, handling and storage, waste management, and cost. Only with an overview of the process will you be able to choose the logistics packaging best suited to the characteristics of your company.
टिप्पणियाँ
एक टिप्पणी भेजें